ProEye CS and ProEye 100 uses a proprietary technique involving strobed LED responses to measure pulp properties in real-time.
- ProEye CS is programmed to measure Consistency only.
- ProEye 100 can simultaneously measure two process variables such as consistency, freeness, ash, and consistency.
These analyzers feature a unique probe design and use four LED back scattering lights in different colors. The calibration process requires correlating measured data with laboratory-determined data.. The analyzer uses advanced mathematics for correlation, regression, and statistical calculations to maintain accuracy in real-time.
ProEye Optical Transmitter Technology
Light Interaction with Pulp
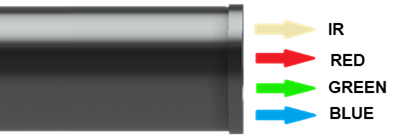
The core principle involes shining an LED light into the pulp, measuring material passing the lens. Depending on the parameter being measured, the light’s interaction with the pulp components will vary. For instance, measuring consistency involves analyzing how much light is absorbed or scattered by the pulp fibers.
Absorption and Scattering
Absorption: If the goal is to measure the concentration of certain chemicals or colorants in the pulp, the transmitter uses the principle of light absorption. Specific wavelengths of light are absorbed by the chemicals, and the amount of light that passes through gives an indication of the concentration.
Scattering: For parameters like fiber consistency, the transmitter will use light scattering. As light passes through the pulp, fibers scatter the light in different directions. The pattern and intensity of this scattering can be used to determine the concentration of fibers.
Sensors and Detection
The transmitter has sensors that detect either the transmitted light (in the case of absorption) or the scattered light. This data is then converted into electrical signals.
Data Processing
These electrical signals are processed using algorithms to quantify the pulp parameters. The precise nature of this processing can vary depending on the specific parameter being measured.
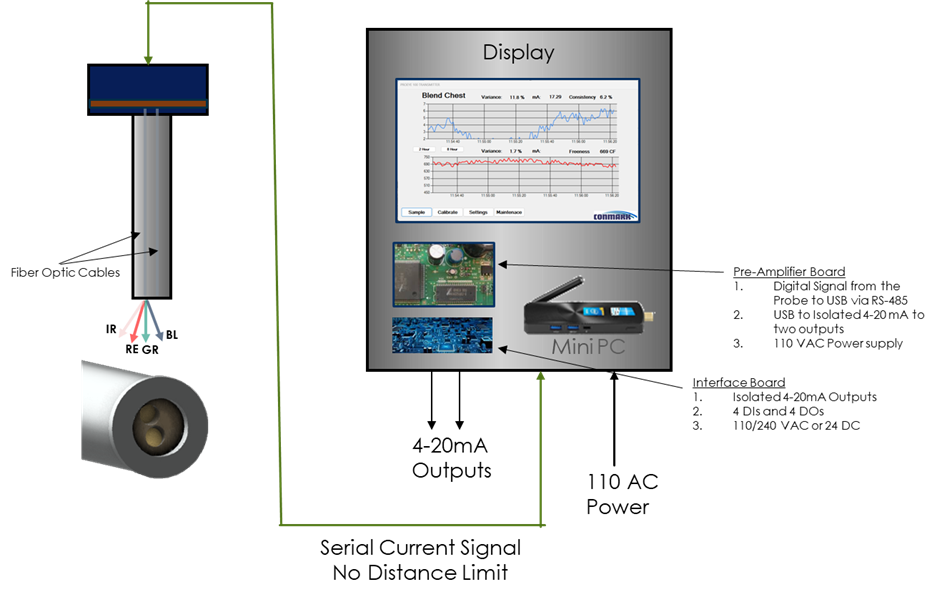
Calibration of Optical Transmitters
Initial Factory Calibration | When the transmitter is manufactured, it is initially calibrated in the factory using standard samples with known properties. This sets a baseline for the measurements. |
Field Calibration | Upon installation in a paper mill, the transmitter needs to be calibrated to the specific conditions and types of pulp used. This involves using pulp samples with known parameters and adjusting the transmitter’s settings until it accurately reflects these known values. |
Calibration Checks | Regular calibration checks are not necessary to ensure ongoing accuracy. On the other hand, significant changes in the pulp, environmental conditions, or process can affect the measurements trigger the need for a new calibration. |
Use of Reference Standards | During these calibrations, reference standards, which are samples with precisely known properties, are used. By comparing the transmitter’s readings with these standards, technicians can adjust the calibration as needed. |
Software Calibration | Modern transmitters also allow for software-based calibration adjustments, where digital processing of the signals is tweaked to align with the known standards. |
The calibration process is crucial for maintaining the accuracy and reliability of measurements, which are vital for the consistent quality of paper production. By understanding the properties of the pulp, operators can make informed decisions about the papermaking process, such as adjusting chemical additives, water content, or processing times.
For more information: [email protected]
To set up conference call: [email protected]
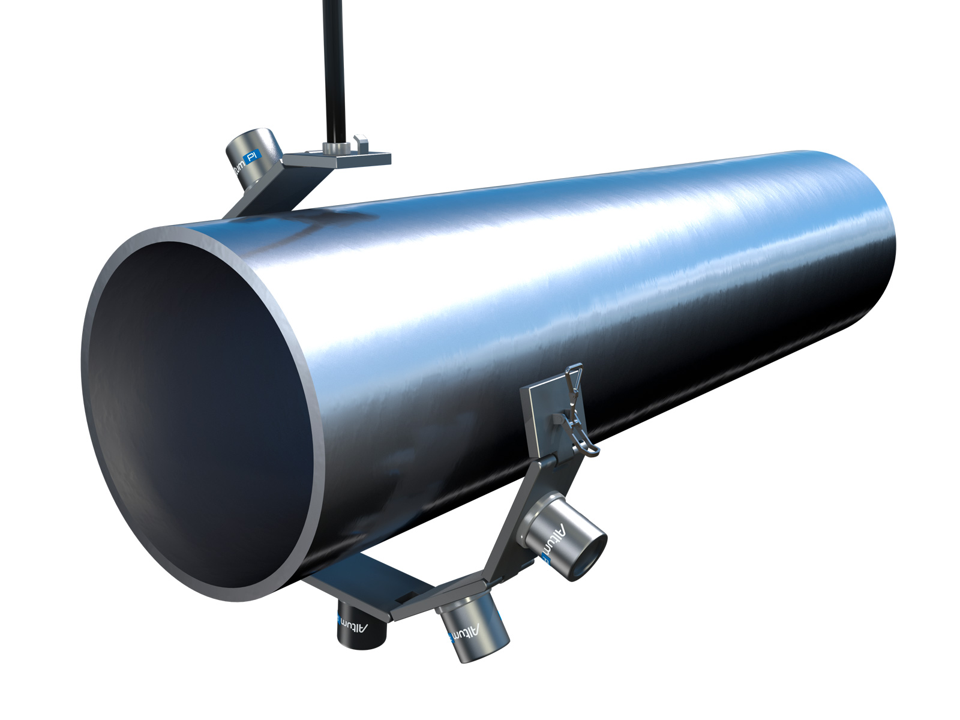
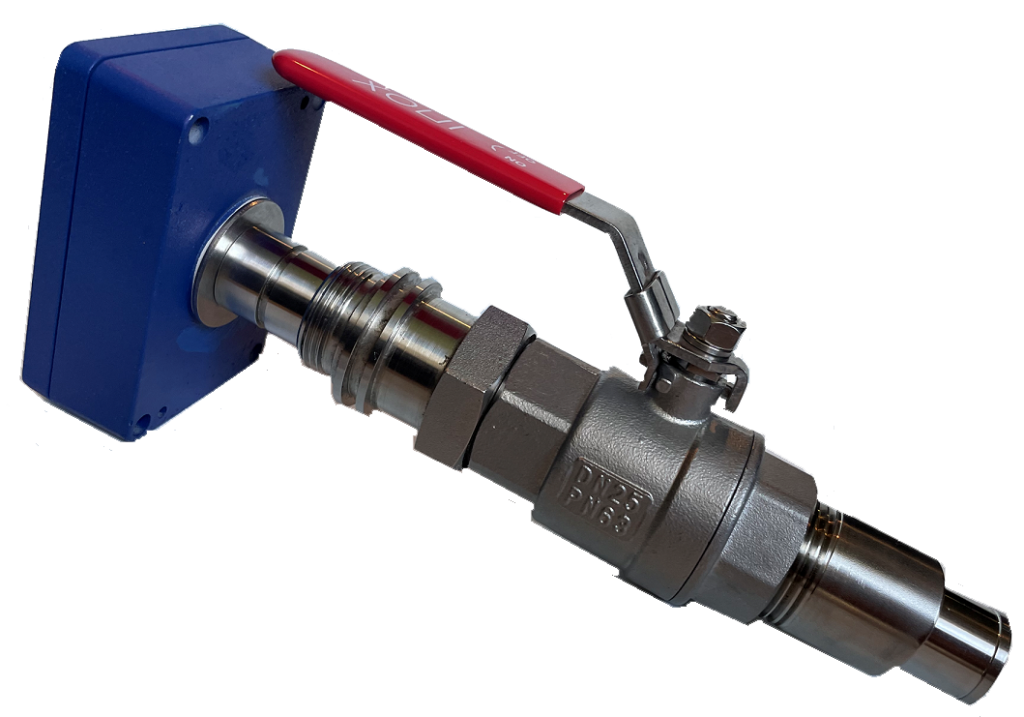
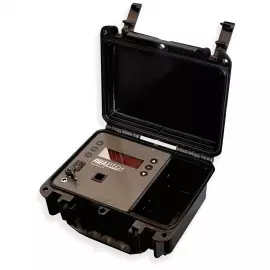
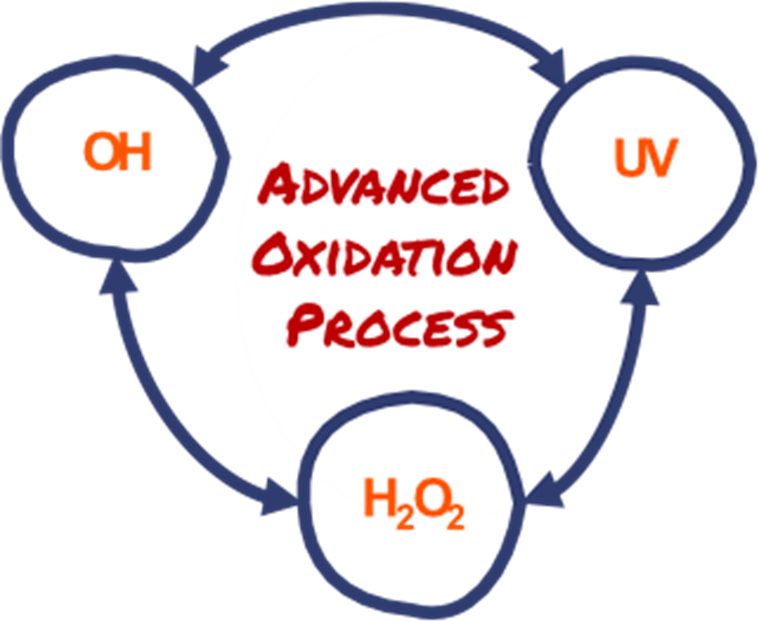
Features and Functions
0 Comments